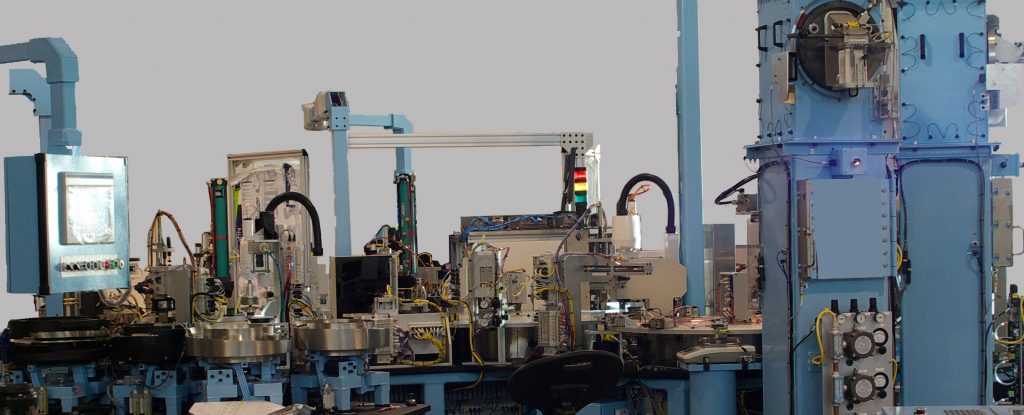
Project details
- Vision-Guided Scara Robot: For product placement based on a multitude of criteria
- Faulty Components: Identification and segregation implemented
- Vision Systems: Identified part compliance and process validation
- Precision Scales: Verified accurate pyrotechnic loading
Setpoint was challenged to design a smaller assembly machine with increased throughput. The customer was moving to a new, facility and needed a custom automated assembly line that allowed them to realize better floor space utilization. Additionally, they wanted a system that could produce more parts.
Setpoint visited the customer’s site to study the existing process and then created a simulation model of the production line to better define the new system and identify potential constraints and problem areas. When the time came for a detailed design, Setpoint’s solution included leading edge technologies applied in innovative ways.
Overall, there were 39 simultaneous operations occurring within a 3 second cycle. To reduce the amount of wiring, Setpoint used Ethernet IP, minimizing controls, diagnostics, and communication lines needed. This meant that less of everything was required to bring a sophisticated line to fruition. At the time, Mike Fielding of Rockwell Automation said,
“It is the most I/O intensive machine in North America.”